(This post has been updated as of September 2023 with an analysis of procurement and software-driven automation opportunities)
The last few years have been a whirlwind of innovation in portions of the supply chain, specifically around logistics – the movement and tracking of goods. In the venture-backed world we have seen major logistics companies created in the freight market, including Flexport, Convoy, and Uber Freight to name a few. We’ve also seen significant company building in the intelligence space, led by P44 and Fourkites.
However, as the logistics innovation cycle matures, we have started to explore other core drivers of the supply chain. One area where we are focusing is on the upstream producers who are extracting raw materials, manufacturing components, or assembling goods. It is this part of the supply chain – what we call the manufacturing stack – that drives the logistics industry and which we now believe is ripe for a re-platforming. Through our logistics investments in companies like FleetOps, Optimal Dynamics, Gearflow and Ocean Freight Exchange, we’ve gained a front-row seat to innovation at either end of the supply chain. And we’ve been tracking how key events – first the pandemic and more recently geopolitical tensions – combined with the growth of digitized data sourcing and robotic automation, have repositioned manufacturing as a sector to watch.
History of Innovation in Manufacturing
In the 1950s, the manufacturing sector employed a third of the labor force in the US and other developed nations. Today that stands closer to 10% of the workforce and roughly the same percentage of GDP. While the manufacturing industry has greatly changed over the past 70 years, much of that innovation was in the globalization of manufacturing (business model), and in the core production techniques (the semiconductor industry is a great example). The manufacturing space was even an early adopter of software for design and planning, but that innovation cycle industry peaked in the 90s, and early aughts led by today’s legacy players including SAP, IBM and Oracle. But, a lot has happened since the 90s – and the manufacturing sector now has some catching up to do.
What’s Happening Now?
Manufacturing in 2022 is not the same as it was in 1950 – and those in the business have a need for stronger productivity and efficiencies than ever before. We are seeing this play out in waves of new technologies aimed at increasing safety, automation, transparency, and data. As these trends continue to grow, we are diving into manufacturing productivity technology as an investment theme, working alongside our LPs to identify what technologies and businesses will truly change the game. Here’s why:
Renewed Push for Reshoring
Conversations around reshoring and nearshoring aren’t new, but the pandemic and strained trade relationships with other nations have created a new urgency for American businesses. For example, the lack of semiconductors from Taiwan & China has put pressure on both U.S. electronics and auto. This has been especially magnified by COVID-19 as auto grew in the US by 90% YoY in 2021. Similarly, the lumber and steel shortage has impacted the construction material supply chain, driving up prices and placing pressure on manufacturers. These current triggers are exacerbating pre-existing issues – such as skilled labor shortages – and manufacturers are unable to keep up with demand. To the South, we are seeing this play out with a massive increase in Mexican manufacturing, with exports up 17.7% YoY to $49.3 billion in October.
Regulation
The current manufacturing landscape has resulted in regulatory action that will both spur industrial growth and increase demand for nearshore goods. For instance, the CHIPS and Science Act is a $50B initiative that funds US semiconductor manufacturing and prohibits fund recipients from expanding operations in select foreign countries including China. Furthermore, the tariffs along with broader economic sanctions have either increased the cost of or entirely restricted the trade of goods, resulting in additional demand for US or nearshore goods. Tariffs on semiconductors, for example, have resulted in a 26% decline in semiconductor imports from China relative to pre-trade war tariffs.
Tech-Empowered Competition and a New Generation of Leaders
Technology focused on manufacturing productivity will be one of the primary solutions to meeting the new wave of demand, and retaining the next wave of managers. Tech-forward manufacturers such as Anduril, Hadrian, and Tesla have set a standard and drive competition within their sectors, pressuring peers to match output. Furthermore, millennials are now replacing both middle and senior management where they have influence over technology investments. The U.S. Bureau of Labor predicts that millennials will make up 75% of the workforce within manufacturing by 2030. Millennials, who are more digitally native, are more likely to drive change and efficiencies with tech solutions than their Baby Boomer predecessors. So our thesis is that innovation in design and process will spill over into other parts of the space – it’s hard to imagine walking out of a digitized production facility and then picking up the phone to place an order with your component supplier, or reading through a paper purchase order from your buyer.
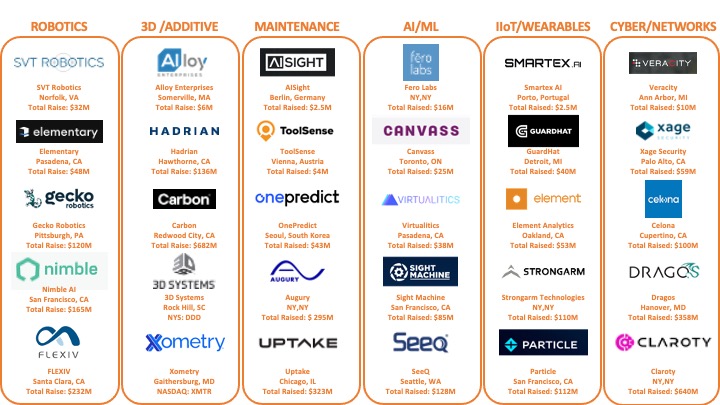
What’s Next?
We expect to see an increase in hardware, software, and hybrid approaches to creating new efficiencies within these markets. We’ve already seen significant advancement in hardware within manufacturing over the past decade. with examples such as Anduril, Hadrian, and Path Robotics all raising significant capital. This foundation of new-age hardware has created a sturdy foundation for more software applications – along with a new appetite for technology-based tools in labor-heavy markets.
We are approaching opportunities in manufacturing with an open mind, but we are particularly excited by the following areas of focus:
1. Robotic automation for the manufacturing and movement of goods. Robotic automation can increase efficiency. With ‘Lights Out Automation’ or fully automated factory production becoming more popular, leveraging technology such as robotics has become a trend. We see an opportunity to invest in software systems and software-first approaches to assist with these technology transitions to the robotic first world with more owners and operators shifting to 24-hour run facilities.
2. Digital Twins are the digital replicas of any process, system, or physical asset with the possibility of building scenarios for better outcomes. In manufacturing, digital twins are built for specific production lines, “real world” scenarios, assets, and even people in production processes. Once digital twins are created they can serve as the singular truth throughout a company’s operation while helping save money, improve production quality, and increase production value. As the industrial sector continues to introduce new connected technologies there will be a need for digital twins to assist in the transition process from the analog world to the digital one.
3. MRO – Maintenance, Repair, Operations. Manufacturers understand that keeping machines healthy and running means everything to the company’s bottom line. However, processes today are outdated, slow, and typically offline and cannot keep up with fast-moving supply chains. Teams are starting to re-envision these practices by bringing new MRO processes and technology. By implementing technology such as modern machines that leverage IoT sensors for data collection or machine learning for data processing, companies can create actionable insights, reduce downtime, and efficiently monitor their expensive equipment.
4. MES workflow or Manufacturing Execution Systems have been the norm in terms of workflow management solutions within the industrial sector. These dynamic systems focus on tracking documents & processes of manufactured goods from raw materials to finished products. However, the majority of operators in the space have been utilizing legacy systems that are not up to speed with the digital age. With cloud connectivity becoming the backbone of future factory floors it is essential for organizations to think about MES solutions that are purpose-built for their production lines.
5. Procurement: Industrial supply chains can be vast and complicated. For example, aerospace supply chains tend to be a convoluted web of OEMs, medium-to-large-sized contract manufacturers, and job shops all interacting with each other simultaneously. When you throw in Defense and Military implications, requirements can become even more complicated as traceability of those parts and systems becomes crucial. It is no surprise to us that we continue to see entrepreneurs creating solutions targeting this problem. Companies like CADDI are building facilities to fill existing demand, while one of our portfolio companies, Volition, is aggregating suppliers to serve as a one-stop shop for all industrial buyers. Procurement is far from solved, and we expect to see more solutions being built in the future.
6. Software-driven Automation: While robotics automation still has ways to go before it saturates the factory floor, there are a few industries where a software-driven approach to automation is feasible. There are a handful of sectors where equipment in a production line is already tech-enabled and a software overlay could manage a task typically supervised by humans. For example there are companies, such as Noodle.ai, that leverage AI to automatically adjust equipment parameters in process manufacturing in an effort to reduce waste and reach optimal yield at a higher rate than an average human. We expect to see similar solutions in sectors with relatively “smart” equipment.
We also imagine with the latest reemergence of AI, we will see ventures tackling the design and programming side of manufacturing that tends to be reliant on tribal knowledge. AI can have a few use cases in the initial design of a complex engineering system, find the most optimal assembly, and provide the most efficient iterations to reach an end goal faster. Many of these tasks today are manual and require substantial man-hours. The potential for automation in these pre-production tasks is there especially for calculation-heavy tasks.
nvp capital is looking for the next great tech-based manufacturing productivity solutions. If you’re building something we should know about, reach out to Sean (Sean@Newark.vc) or Chika (Chika@Newark.vc) with a pitch!